Yeti Rambler Tumblers have become a popular choice for keeping drinks hot or cold for extended periods. These high-quality tumblers are made with precision and attention to detail. The manufacturing process starts with selecting the best materials and then involves a series of steps that require skilled craftsmen and advanced equipment. In this article, BulkFlask, a leading wholesale rambler tumbler manufacturer in China, will explore the detailed process of how Yeti Rambler Tumblers are manufactured, from the preparation of materials to the final packaging of the product. Now you can follow BulkFlask to take a look at these interesting producing steps!
1. What is the processing of Yeti rambler tumblers?
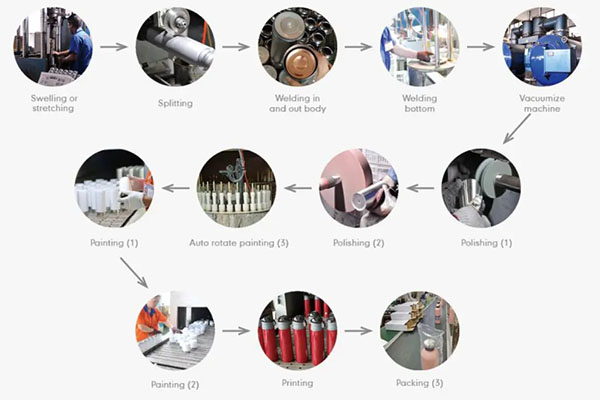
As we all know, the Yeti rambler tumbler is a kind of insulated double-walled water bottle. And almost all the double-walled insulated water bottles have similar structures, double stainless steel walls with vacuum insulation. In general, Yeti rambler tumblers are manufactured from 9 processes: raw material → outside wall → inner wall →double walls combination → vacuum processing → polish inner and outside wall → coating → logo/pattern/text printing → assembling → testing → packaging. Here we’ll show you in detail:
1.1 What materials does Yeti rambler tumbler choose?
- Stainless Steel: The inner and outer walls of the tumbler are typically made from 18/8 stainless steel. This type of stainless steel contains 18% chromium and 8% nickel, which enhances its durability, corrosion resistance, and ability to retain temperature.
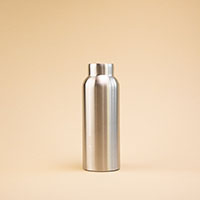
- BPA-Free Plastics: While the main structure of the tumbler is made from stainless steel, some components, such as the lid and seal, incorporate BPA-free plastics. These plastics are chosen to ensure that the tumbler is safe for use with beverages and does not contain any harmful chemicals.
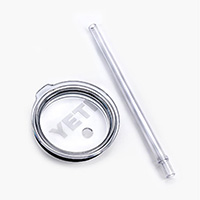
1.2 How is the outside wall of Yeti rambler tumbler manufactured?
- Pipe Cutting: These pipes are cut into appropriate lengths to create the desired height of the tumbler.
- Pipe Shaping: After cutting the pipes, they may go through additional shaping processes to achieve the desired contour or curvature. This could involve techniques like bending, rolling, or forming the pipes to match the intended design of the tumbler.
- Raw Tumbler Splitting: If the tumbler is initially manufactured as a single piece (e.g., a cylinder or tube), it may undergo a splitting process to separate the outer and inner walls. This splitting can be done using specialized tools or machinery.
- Surplus Part Removal: Once the outer and inner shells are separated, any surplus material on the top of both the outer and inner walls is cut off or trimmed to achieve the desired height or shape of the tumbler.
- Rim Smoothing: Grinding, sanding, or polishing to create a smooth and even surface on the edges of the tumbler walls.
- Circle Rib on the Bottom: To enhance stability and structural integrity, a circular rib or reinforcement may be added to the bottom of the outer shell. This rib provides support and strength to the tumbler’s base.
1.3 How is the inner wall of Yeti rambler tumbler manufactured?
- Cutting: The stainless steel plates are cut into small round pieces, typically matching the size and shape required for the inner wall of the tumbler.
- Deep Drawing Process: Deep drawing involves placing the steel piece into a mould or die and applying pressure to shape it into the desired form. This process allows for the creation of a seamless inner shell.
- Surplus Part Removal: Cut off or trim to achieve the desired height and shape of the tumbler.
- Rim Smoothing: Grinding, sanding, or polishing to create a smooth and comfortable edge.
- Copper Plating: Copper plating is applied to the inner and outside surface of the stainless steel to enhance certain properties such as corrosion resistance or heat conductivity. Copper plating can also provide an aesthetic finish.
1.4 What is the combing process of inner and outside wall?
- Inner Wall Insertion: The inner wall is carefully placed inside the hollow space of the outer wall, ensuring a proper fit.
- Alignment: The inner and outer walls are correctly aligned to ensure that they are concentric and centred within each other. Also, space for a vacuum will be left.
- Attachment: Welding can securely attach the inner and outer walls.
1.5 What is vacuum processing of Yeti rambler tumbler?
- Preparation: The semi-tumblers, typically 80-120 pieces per batch, are placed on a steel tray. The tray is arranged with the top side of the semi-tumblers facing down and the bottom side facing up.
- Solder Placement: A small piece of solder is positioned at the location of the vacuum hole in the middle of each semi-tumbler. The solder is designed to melt when the temperature reaches 900 degrees Fahrenheit (482 degrees Celsius).
- Vacuumize Oven: The tray containing the semi-tumblers is placed inside a vacuum oven. The oven is designed to create a vacuum environment for the tumblers.
- Heating Process: The oven is set to the appropriate heating temperature and time. The heating process begins, gradually increasing the temperature inside the oven.
- Air Exhaustion: As the temperature reaches approximately 600 degrees Fahrenheit (316 degrees Celsius), the air inside the gap between the inner and outer shell of the tumbler starts to be exhausted over time. This process helps achieve a high vacuum rate, reaching 99.999% in the gap between the inner and outer walls.
- Solder Melting: Once the desired vacuum rate is achieved, the oven temperature is increased to 900 degrees Fahrenheit (482 degrees Celsius). At this temperature, the solder placed on the bottom of the semi-tumbler melts, sealing the vacuum hole and maintaining the vacuum inside.
- Cooling Down: After the solder melts and seals the vacuum hole, the oven stops heating and begins to cool down. This allows the tumbler to stabilize and complete the vacuum processing.
- Vacuum Rate Checking: The final step involves checking the vacuum rate of the completed tumblers to ensure they meet the required standards. This step ensures the quality and effectiveness of the vacuum insulation.
1.6 How does Yeti rambler tumbler polish inner and outside wall?
- Surface Preparation: Before polishing, the inner and outer walls of the tumbler may go through a cleaning process to remove any dirt, oil, or debris from the manufacturing process.
- Rough Polishing: The initial stage of polishing involves using abrasive materials or tools to remove any surface imperfections or roughness. This process helps to create a more uniform and smooth surface.
- Finer Polishing: Once the rough polishing is complete, finer polishing steps are employed to further refine the surface. This may involve using finer abrasives or polishing compounds to achieve a smoother and more lustrous finish.
- Buffing: Buffing is a common technique used in the polishing process. It involves using a rotating buffing wheel or pad along with polishing compounds to achieve a high shine and smooth texture on the surface of the tumbler. The buffing process helps to remove any remaining scratches or imperfections. Sometimes, electro-polishing will also be adopted to get a better surface. Electro-polishing is an electrochemical process that is commonly used for the polishing and smoothing of metal surfaces. It is particularly effective for stainless steel materials, which are often used in the construction of tumblers like the Yeti Rambler.
1.7 How to coat and print logo on Yeti rambler tumbler?
- Coating Process: Powder coating is a popular method used for applying a durable and protective finish to the outer wall of Yeti Rambler Tumblers. In this process, a dry powder coating material is electrostatically applied to the tumbler’s surface. The coated tumbler is then heated in an oven, causing the powder to melt and form a smooth and even coating. Powder coating offers excellent durability, resistance to scratches, and a wide range of color options.
- Printing Process: Screen printing is a popular method for applying logos and designs to Yeti Rambler Tumblers. In this process, a screen with the desired logo or design is placed on top of the tumbler’s surface. Ink is then pushed through the screen using a squeegee, transferring the design onto the tumbler. After printing, the ink is typically cured through heat treatment or air drying.
1.8 How does assembling, testing and packaging work?
- Tumbler Body Assembly: Attach the insulation material to the inner walls of the tumbler body. Apply sealant to ensure a secure bond between the insulation and the tumbler body. Allow the sealant to cure or dry as per the manufacturer’s instructions.
- Lid Assembly: Combine the lid with a tumbler. Make sure that every lid matches its tumbler.
- Testing: This involves leak testing the lid and ensuring proper insulation to ensure quality and functionality.
- Packaging: Once the tumbler has been assembled and tested, it is ready for packaging. The packaging process involves placing the tumbler in a protective sleeve or wrapping it with a protective material to prevent scratches or damage during transit. It is then placed in a box along with any accompanying documentation, such as user manuals or warranty information.
It is not the ending now. Before finalizing the packaging, conduct a final quality control check to ensure that the tumbler meets all the required standards. This can include visual inspections, functional tests, and verifying that all necessary components are included. Then apply any required labels or stickers to the packaging, including product information, barcodes, and safety warnings. Finally, prepare the packaged tumbler for shipment by arranging it in larger boxes or crates, ready for distribution to retailers or customers.
2. Where is Yeti Rambler Tumbler produced?
Yeti has utilized manufacturing facilities in China to produce its products, including the Yeti Rambler tumblers, taking advantage of China’s cost efficiency, expertise in manufacturing, and well-developed supply chain network. China’s lower labor costs have provided cost savings for Yeti and allowed them to produce their products more competitively. China’s manufacturing expertise, skilled workforce, and advanced infrastructure have ensured high-quality production for Yeti. Additionally, China’s extensive supply chain network has facilitated efficient access to raw materials, components, and specialized manufacturing services, contributing to streamlined production processes. While manufacturing locations can change over time, China’s historical prominence as a global manufacturing hub has made it a preferred choice for many companies, including Yeti.
If you want more information, please contact us!